Updates & Blog
GUEST BLOG: Would Wood Work? Builders Eye Mass Timber for Construction, Conservation.
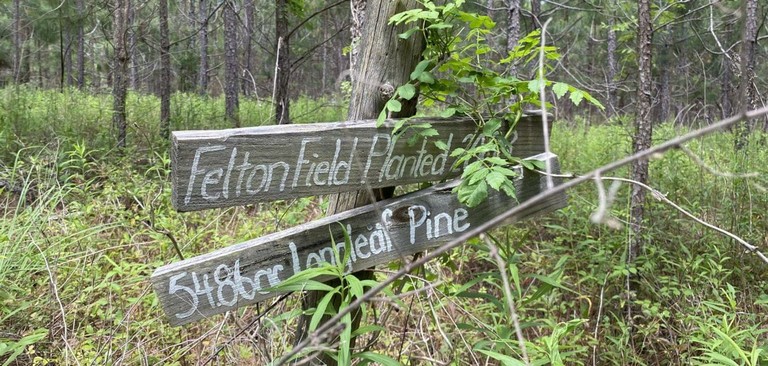
This article originally appeared on July 14, 2021 on the U.S. Fish and Wildlife Service website.
Hawkinsville, Georgia – Dr. John Bembry roams his 2,200-acre tree farm pointing out the ecological wonders bestowed by “the good Lord.”
Here, he says, is an age-old longleaf pine stand towering over wiregrass and gallberry scrub. There’s a gopher tortoise whose sandy burrow provides shelter for hundreds of creatures. And that cypress-kneed swamp – Bembry prefers “mill pond” – is filled with bass, bream, catfish and white perch.
“I’ve always had a very strong environmental ethic. It comes from my heart and from a religious perspective,” the veterinarian says. “But you can have the best of intentions and it doesn’t matter what you do if it’s not economically sustainable.”
Therein lies the dilemma faced by many a conscientious tree farmer – how to do good by doing well. Bembry and other southern growers, industry leaders, government officials and environmentalists have latched onto a solution.
Mass timber.
Otherwise known as engineered wood, cross-laminated timber or nail-laminated timber, mass timber, increasingly, is used to build buildings. It is all the rage in the pinelands of the Deep South and the chat rooms of climate activists. It’s not often that rural tree farmers see eye-to-eye with urban tree huggers. Yet the former wants to save an industry hit hard by over-supply and low prices. The latter wants to save the world.
Trees suck up climate-killing carbon dioxide, and the bigger they grow, the more they potentially benefit the atmosphere. Mass timber – think of 20 pieces of laminated pine glued or nailed together into a board or a beam – replaces climate-damaging concrete or steel in the construction of offices and apartments.
“Our southern forests have a huge role to play in sequestering carbon in the wood and fiber they produce,” says Leopoldo Miranda-Castro, the regional director for the U.S. Fish and Wildlife Service in the South Atlantic, Gulf and Mississippi Basin. “If managed correctly, these forests also provide great habitat for a variety of at risk, threatened and endangered species. We need healthy working forests to do conservation in the South. These species depend on it.”
Mass timber, of course, has its drawbacks, none larger than the public’s perception that wood is weaker – and more flammable – than concrete or steel.
“And people have heard for a long time now that it’s a bad thing to cut down trees because they’re important for carbon sequestration, conservation and everything else,” says Scott Davis, project director for Keeping Forests, a coalition of southern forestry, corporate, nonprofit and governmental agencies. “But trees are, in fact, a renewable and sustainable resource. And when they’re cut, nearly all of the time, they’re replaced by another tree.”
Storing carbon
During the pandemic, when factories were closed and cars stayed in garages, greenhouse gas emissions – the main contributor to the warming world – dropped 6 percent. The reprieve proved short-lived. The amount of carbon dioxide shot into the atmosphere from cars, trucks, coal plants, cement makers, deforestation and agriculture has since returned to historically high levels. The federal government’s goal of slashing carbon emissions in half by 2030 will require life-altering changes to the fossil-fueled American way of life.
But there’s a roadmap to a carbon-free future that, in addition to targeting the industrial and transportation sectors, focuses on new markets in the construction and building industries. In fact, the manufacture of steel, cement and glass, along with transportation of the materials, accounts for 11 percent of all global greenhouse gas emissions, according to the International Energy Agency.
Trees act as a “carbon sink,” pulling tons of carbon dioxide from the air. When cut, though, they release some of that carbon back into the atmosphere. Digging up the soil surrounding trees also sends carbon dioxide skyward. Transportation, and turning a tree into 2-by-4 planks, also adds to the greenhouse gas pile.
Yet some carbon remains embedded in mass timber, stored for a century or longer. A green-building industry study in 2019 estimates that one cubic meter of cross-laminated timber sequesters one ton of carbon dioxide.
“Lumber is, basically, a carbon-storage unit,” says Tim Lowrimore, the state forester for Georgia. “Mass timber provides a solution to one of the toughest challenges our country faces – climate change.”
And, maybe, an answer to a questionable future for the South’s tree farmers. Forests cover nearly 250 million acres across 13 Southern states, the fastest-growing region in the country. As the population booms, the U.S. Forest Service predicts, as much as 23 million forested acres will be lost to development and agriculture by 2060. Not only would the lumber industry suffer, but the ecosystem services that forests provide – clean air and water, recreation, plant and animal conservation, carbon sequestration – would disappear too.
“These are services that forests provide to all of us, but the forest landowners are currently not being paid for them,” says Davis, whose partnership aims to help the timber industry as well as the environment. “It’s a service that has real economic value and we’re currently getting it for free. We need to develop markets for those services, and the products that come out of them, so we can properly compensate the landowner.”
Growers are already under the gun. An over-abundance of trees from the Carolinas to Texas had mills paying the lowest prices for logs in decades, though prices have rebounded a bit recently. Not even the pandemic-infused surge in home construction and remodeling dents the woody supply. And growers with a marked conservation ethos, like Dr. Bembry, are hurting even more.
About a quarter of Dr. Bembry’s farm today is long-living, wildlife-friendly longleaf pine. The veterinarian lays fire to all his longleaf every two or three years, ensuring perfect habitat for eastern indigo snakes and gopher tortoises. Tortoise burrows are flagged before any trees are harvested.
“To be perfectly honest, I hate to cut trees,” Dr. Bembry says, laughing, while maneuvering the F-150 between stands of loblolly and slash pine. “But what better use for land is there than growing trees? You want a parking lot instead?”
‘Ways to go’
Shan Arora doesn’t. He wants beautiful buildings.
“Buildings should be like flowers,” says Arora, a new-age evangelist of renewable and sustainable development. “Things that have beauty we tend to take better care of.”

He’s the director of the airy and bright Kendeda Building for Innovative Sustainable Design on the campus of Georgia Tech in Midtown Atlanta. It’s a marvel of mass and recycled timber and glass with an apiary, pollinator garden and blueberry orchard on the roof. Glue-laminated columns and beams help support the Kendeda Building in place of concrete and steel. The yellow pine came mostly from Arkansas. The floors are made of nearly 500 nail-laminated panels with the bulk of the wood sourced in Alabama and the rest salvaged locally.
The 37,000-square-foot structure, billed as “the greenest classroom building in the U.S.,” cost $25 million, about 13 percent more expensive than a comparable Georgia Tech building. But the high up-front construction costs will be mitigated by long-term savings on energy and water.
“Look at this beam,” Arora says while touring Kendeda. “It is a precision product that has the potential to create manufacturing jobs in our state. And, as we build more buildings with mass timber, we have the opportunity to grow more timber in Georgia.”
Only two Atlanta buildings, including an office in the nearby Atlantic Station development, use mass timber. A third, at Ponce City Market, is planned. Nationwide, nearly 400 mass timber projects have been built, according to the forest service. More than 500 are being designed.
Yet there remains a paucity of mills cutting and assembling mass timber and most are in the Pacific Northwest. A mill in Dothan, Alabama, is the South’s only mass timber manufacturer. It opened after the Kendeda Building was underway.
“We’ve got a bit of a ways to go,” says Lowrimore, director of the Georgia Forestry Commission. “It’s a new technology. Building owners and architects are interested in it. But we’ve got to get builders and contractors to be willing to adapt and use mass timber.”
The International Code Council, which sets building standards, now allows wooden buildings to rise 18 stories. Georgia legislators approved a bill a few years ago prohibiting cities from outlawing mass timber in construction. Lowrimore and others expect corporations, and their financiers, to get on the mass timber bandwagon as more stringent anti-carbon laws hit the books. Walmart, for example, is building its new headquarters in Arkansas with 1.1 million cubic feet of cross-laminated timber.
Forests, and forest products, capture and store 10 percent of all annual U.S. carbon emissions. And in the South, where upwards of 80 percent of forested lands are privately owned, conservation doesn’t get done without economically sustainable “working forests.”
“It’s always a good thing when industry and conservation find common ground,” says Miranda-Castro, the Service’s regional director. “Well-managed, working forests help conserve the land, water and air we all depend upon for healthy lives. Mass timber is a win for people, fish, wildlife, and plants.”